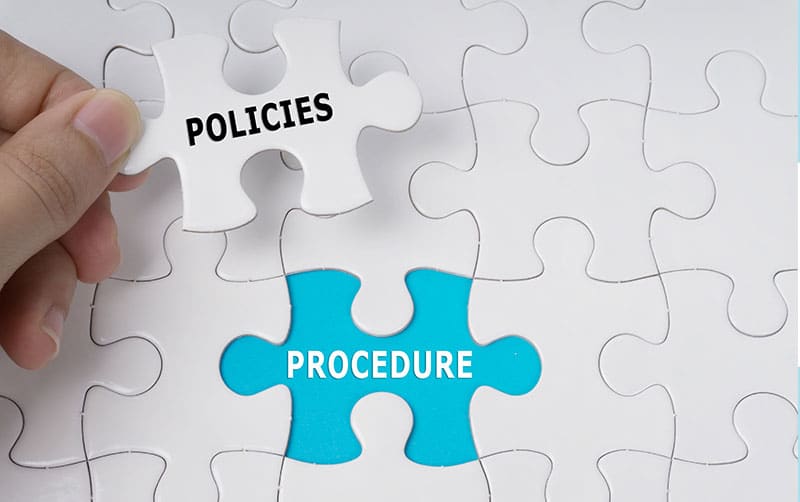
Safety Spotlight
Writing Procedures
By: Jim Poage
QUICK RECAP
In the first installment, we learned how to recognize workplace hazards by using a job hazard assessment to evaluate work activity as it is taking place to recognize risk factors. In the second installment we learned to evaluate the hazard for the best method of controlling it by using the Hierarchy of Controls. In the third installment we discussed the different OSHA standards that applied to the workplace according to the 1910 General Industry Classification or the 1926 Construction Classification by referencing the standards to the North American Industrial Code that all businesses operate under. Now we are going to prepare to begin writing our safety policies.
WHERE DO YOU START?
Utilizing the information found in the 1910 General Industry Standard or the 1926 Construction Standard (which ever applies) it should be fairly easy to construct a procedure for each job that had a recognized hazard by the activity that was being performed. In the standards, there are topics such as forklifts, chemical handling, material handling, and fall prevention. Each one of these can be broken out and applied to a specific activity being done in the workplace.
If you look at both the 1910 in the 1926 standards for the topic of fall protection, you will notice that there is a difference in when fall protection needs to be provided. In the 1926 standard depending on the type of construction that is being performed fall protection has to be provided for employees at different intervals such as six feet above elevation, eighteen feet above grade, and at certain other points during specialized construction such as steel erection.
If you look at the general industry standard it specifies that anything over four feet in height above grade or above elevation requires fall protection. If fall protection is so important why isn’t it the same height requirement in both general industry and construction? The reason for this is the type of work activity that is being performed. In construction obviously there are times when people must work at elevations where it is more difficult to protect them from a fall then in general industry.
A lot of general industry involves activities such as retail business activity where the greatest risk may be portable ladders or step stools. This should explain the importance of knowing which standard you are required to work under.
NEXT STEPS
So now that you’ve identified the standard you are covered by, and you’ve gone through and found the sections of the standards that apply to the specific activities in the workplace, you can begin to write procedures. There are thousands of examples of procedures on the Internet. Most start with a title, followed by a purpose which identifies who is being addressed in the procedure and for what reason. It then leads into a procedure that is broken down into specific steps or into explanations that an employee would understand.
There is a shortcut to all of this. Find a procedure already in use by another company in your same industry, then edit it to make it fit your need. There are some state plans like Washington that actually provide editable procedures for employers to use.
WE’RE HERE TO HELP
Many equipment manufacturers will provide a basic procedure when you make a purchase. Even if you go this route, you need to understand how to prepare a procedure, just in case, there isn’t one readily available. Should you need a copy of a procedure or an example to follow, please do not hesitate to contact me.
For more information about how to prepare a safety procedure contact Jim Poage, jimpoage@formetco.com or 678-951-1132.